Oreo De-Creamer
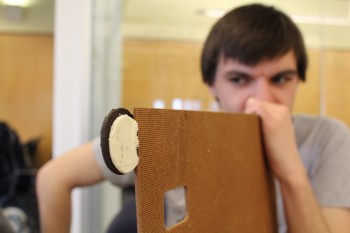
Silly? Yes. Functional? Not really. Worth making? Absolutely.
This was the first device created by Tufts MAKE; an extracurricular product design club that I helped start as a college sophomore. Despite its outward appearance, this device ended up becoming one of the most important projects of my Tufts career.
Figuring out how to de-cream an Oreo provided our small group of 6 students with an opportunity to practice an iterative product design process at a time when Tufts' workshops were largely off-limits to underclassmen. With the support of our faculty advisor and Human Factors professor Dan Hannon, we ended up pushing the boundaries of making at Tufts and encountered barriers that I would spend the rest of my time in college trying to break down via the Maker Network.
Getting started
During my first semester of sophomore year as a newly-minted Human Factors major I mentioned the possibility of starting a product design club to my faculty advisor, Dan Hannon. The Tufts Mechanical Engineering department was just beginning to discuss expanding opportunities for student-led extracurricular making at the time, so my timing was particularly good.
Dan wisely suggested that I treat the potential club as a prototype in itself by coming up with a small-scale project idea that students would enjoy working on. Nabisco was running a goofy Oreo Separator ad campaign at the time, and after seeing a video of their machine I thought that an Oreo De-Creamer project would offer an ideal blend of solution diversity, experimentation, and fun. Dan agreed.
In the wake of my InvenTech experience, I knew that emphasizing the process over the product and effectively organizing each meeting would be vitally important in the face of so many unknowns. I had recently read about the 5-Day Product Design Sprint Process (codified by Jake Knapp at Google Ventures) and decided that the structure it provided would be perfect for our small product design experiment.

The Google Ventures Design Sprint process
Dan encouraged his classes to join, and 5 students attended the preliminary meeting. We agreed to start our sprint right after our Spring Break, giving us roughly 5 weekly meetings to complete the project before our final exams. Dan allowed us to use his lab as a meeting space, paid for our first round of Oreos, and arranged for the Mechanical Engineering department to reimburse us for a small amount of supplies.
After coordinating all of the above, our team was ready to hit the ground running.
Practicing a design sprint
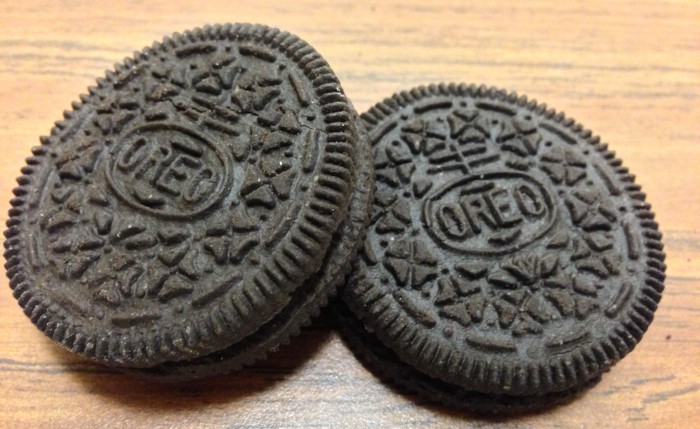
Understand & Diverge
Although the official Design Sprint process distinguishes between these two steps (1 and 2), the extremely limited commercial viability of de-creaming Oreos and our group's intent to learn rather than compete allowed us to condense the two into one.
We agreed from the outset that our goal was to practice the Design Sprint process by creating at least one or two prototypes that were capable of de-creaming an Oreo cookie. After some brief introductions and opening up our first bag of ceremonial cookies, I passed out some sticky notes and we began to "Diverge".
First we broke down what the process would look like into 3 general steps; inserting the cookie, removing the cream, and then producing the end result. We generated a list of possible end products including 1 large stack of cookies, 2 smaller stacks of cookies, a giant glob of cream, 3D-printable extruded cream, crumbled Oreo cookies for ice cream, and so on.
Then we started to independently consider all of the possible ways we might be able to insert the cookie into our device; maybe with a sled, through a slot, with a gun mechanism, and more. We came back together to organize our ideas into general groups, and moved on to the second step: removing the cream.
As anticipated, we started to realize that there were some properties of Oreo cookies that we were unsure about. Does Oreo cream melt in an oven or a microwave? Does it adhere to one side more than the other when pulled apart? Would the whole thing catch on fire if we exposed it to a blow torch?
In order to decide on an approach for our first prototype, we needed to do some testing to see which method was the most effective way of de-creaming an Oreo.
Decide
Could we twist the cookies off of the cream?
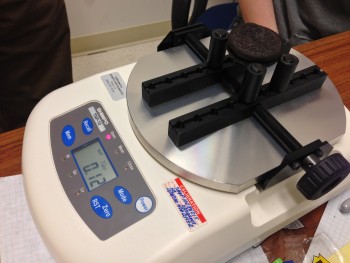
Sort of. We found that the cream of an Oreo tends to be more stuck to one cookie than the other, likely as a result of its manufacturing process. We used one of the Human Factors department's force measuring devices to quantify the torsion force required to twist the cream off the cookie, and although one of the two cookies would occasionally twist off cleanly, predicting which cookie that would be wasn't possible. Without being able to determine which cookie half would end up with cream stuck to it, we passed on this method.
Could we melt the cream away?
No, but we sure tried! The sugary cream and the outer cookie seemed to have similar melting points, so separating them with heat wasn't easy. Using an open flame wasn't effective at all, and the microwave ended up melting just as much cookie as cream, creating a goopy mess.
Could we scrape or push the cream off the cookie?
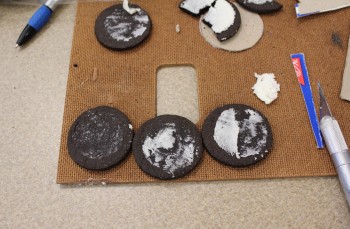
Yes, for the most part. We tried slicing off the cream with an X-ACTO blade, and although it left some residual cream behind, the result was more consistent and effective than the other two methods.
Looking at our idea board, we suspected that pushing or extruding the cream through the gap between the two cookies could be an effective method of separation, particularly since the size of each cookie is much more standardized than the amount of cream in the cookie or its overall dimensions.
After experimenting with these methods and learning much more about the flame resistance of Oreos than anticipated, we re-grouped and agreed to try building a device that could slice/cut/push the cream between two Oreos.
Prototype
This was the most difficult part of our project. After an unfortunate accident at Yale University in 2011 involving a spinning lathe, many schools across the country heavily restricted access to their labs without completing mandatory safety training and signing waivers. As sophomores our access to even basic hand tools was restricted, so we had to buy and use our own as safely as we could.
We picked up some basic wooden parts from our local hardware store in an attempt to create an Oreo-holding clamp that could hold the cookies in place while we extruded the cream, but it quickly became clear that wood was both too flexible and difficult to clean for our project. The dimensions of Oreo cookies were very precise and matching that precision in wood without the necessary tools was too difficult.
Thankfully, our advisor was able to coordinate with the Mechanical Engineering department's machine shop to get us supervised access to their laser cutter. We ordered a few sheets of clear acrylic and designed a multi-layered assembly that would precisely hold the two cookies in place while an extruder pushed out the cream. This was the first time any of us had seen or used a laser cutter before, so seeing it action was quite cool. We were also able to use the shop's electric drill and clamps to finish putting together our earlier wooden prototype.
Validate
So did it work? If we pushed the wedge-shaped acrylic extruder through the device very carefully, sure! The top and bottom pieces held the cookies in place while the cream was squeezed out between them. The device did get pretty messy, and removing the de-creamed cookies required disassembling most of the device, but it got the job done.
More importantly, however, was that our group had met our goal of steadfastly practicing the product design process. Each meeting had a purpose, we documented and tested our ideas along the way, and we succeeded in creating multiple prototypes over the course of the 5 meetings we agreed to. From a logistical and club-forming perspective, it was the success we needed to take our next steps.
Takeaways

An article about Tufts MAKE in the Tufts Daily on November 18th, 2013
We knew from the beginning that our Oreo De-Creamer would ultimately be useless as a device, but the process of creating that Oreo De-Creamer made it an important artifact of its time. We succeeded in practicing and learning about the product design process, and the many barriers we encountered became the inspiration for Tufts MAKE's higher goal of sparking school-wide cultural change.
This early product design practice also helped our members during their sophomore internship interviews, as one of my teammates described for the Tufts Daily:
“I applied for my first internship last summer at athenahealth and we had to present a portfolio during the interview, and I talked about the design process we went through to make the Oreo de-creamer,” Kuperman said.
She showed the team pictures of the different iterations and the cardboard prototype she had made to inform the final design of the Oreo de-creamer.
“During the interview they said that the design process that I described was exactly the design process that they use, and I’m sure that helped me get the job,” Kuperman said. “Knowing the design process is important and does set you apart from other applicants.”
For me personally, the success of this project meant that the skills I learned through InvenTech were already helping me to succeed at Tufts. Breaking down the barriers that I encountered while trying to help my team succeed became the unwritten mission of both Tufts MAKE and the Tufts Maker Network later on, and I like to think my work helped to slightly accelerate the transformation of Tufts' maker culture into what it eventually became.