Baby BB-8
Creating a functional BB-8 droid was my last project as Tufts MAKE's leader and an excellent example of the kind of interdisciplinary learning and collaboration that our club was founded to support.
Our small team of 6 underclassmen with backgrounds in Mechanical Engineering, Philosophy, Computer Science, Electrical & Computer Engineering, and Human Factors worked together for 2 months to try and create a BB-8 that could roll across the floor just like in Star Wars: Episode VII. Doing so required each of us to share our skills and learn alongside one other to create and assemble each of its components.
In classic Tufts MAKE fashion we started this project with very little background knowledge and finished it with far more problem-solving and equipment experience than we anticipated.
Inspiration
Soon after the release of Star Wars: Episode VII in December of 2015, home-made recreations of the lovable BB-8 droid started to circulate around the tech news circuit. One in particular caught my eye. Using inexpensive components like a beach ball and deodorant rollers, 17-year-old Angelo Casimiro was able to create a fully-functional model for roughly $120.
The diversity of skills, tools, technologies and materials required to create a BB-8 prototype seemed to make it a perfect project for Tufts MAKE. After successfully kicking off Spring 2016 with the Weekend of Making I announced the new project idea in our club newsletter and coordinated with the managers of Jumbo's Maker Studio to use it as our meeting space. Six new Tufts MAKE members and I created a detailed plan, ordered the parts, and started building.
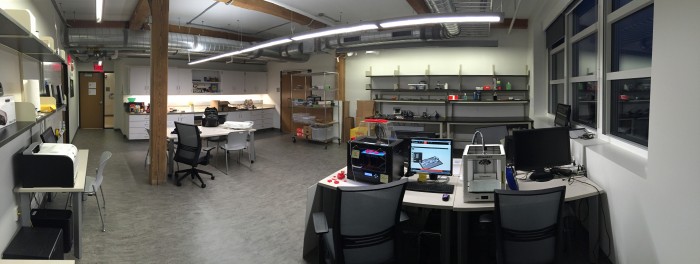
Jumbo's Maker Studio in Tufts' new Collaborative Learning and Innovation Complex [CLIC]
Goals
- Make a BB-8 that can roll around and make sounds
- Finish within 2 months, or roughly 7 meetings
- Learn about electronics, coding, 3D printing, soldering, and laser-cutting along the way
- Have fun
Just like the Oreo De-Creamer and Tufts Dash projects before it, we agreed from the get-go that "learning through making" was more important to us than creating a perfect prototype.
Process
Making the fiberglass body
We decided to use a beach ball for BB-8's body just like Angelo's design, but instead of paper maché one of our team members on Tufts' rowing team offered to show us how to make fiberglass in Tufts' Boat House.
We learned about the structural properties of fiberglass and cut out two layers' worth of fiberglass cloth to ensure that our ball was strong in every direction. Our team member showed us how to (safely) mix resin with hardener and apply the damp fiberglass to our beach ball's rounded surface. It took 12 pieces and 2 hours of careful mixing and positioning to finish our ball and leave it to harden.
One week later we returned to grind the ball's surface with an air-powered sander and smooth it out with finer-grained sandpaper. The ball was still very bumpy, so we brought it back to the Studio and filled in major dents with wood putty. We sanded it one last time, carefully cut it in half with a dremel tool, and spray-painted the outside of the ball with white spray paint.
3D printing parts
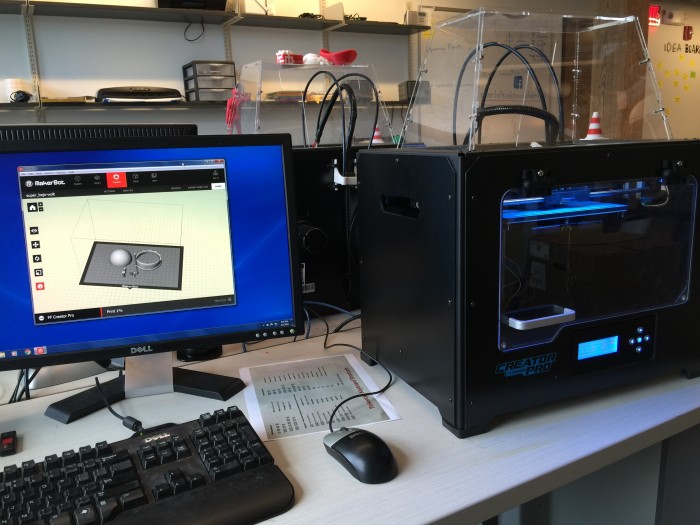
Most students in our group hadn't used 3D printers before, so I demonstrated the basics of using simple 3D modeling tools like Tinkercad to create printable parts with the Maker Studio's FlashForge Creator Pro and Ultimaker 2. We ended up finding pre-made components for BB-8's eye, holoprojector, and antenna on Thingiverse, so we used those to save time. To make the eye shiny, I showed the group how isopropyl alcohol could be used to smooth and melt away the ridges of 3D prints.
Not measuring twice
After hot-gluing BB-8's 3D printed parts onto its foam head and placing it on its body, we noticed that something looked a little off. Its head was huge!
It turned out that the beach ball we ordered from Amazon wasn't actually 20 inches in diameter as the page claimed. Sure enough, just a week after we ordered it, another user noticed the same thing and left a bad review.
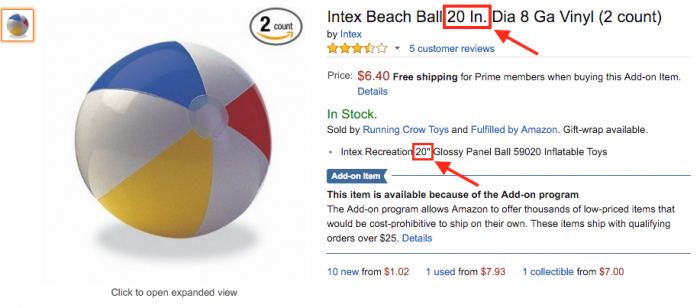
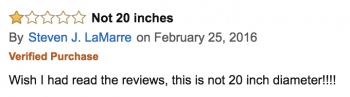
Our workaround? Re-naming our prototype "Baby BB-8" in preparation for the character's inevitable inclusion in a future Star Wars installment. Ahem.
Building the platform
Our next task was to assemble the inner platform that would hold together Baby BB-8's motors, battery, ball casters, and magnetic platform that would keep its head in place. Using math and some expert-level eyeballing we laser-cut pieces of acrylic and dremel-cut a few metal shoe rack bars to position the magnetic platform just below the inside edge of the ball's shell.
Assembling the electronics
Our Electrical & Computer Engineering and Computer Science students led Baby BB-8's electronics work and helped teach our other members the basics of soldering and electronic components. They wired up our Raspberry Pi 3 to brushless motors through a motor driver and wrote a basic Python script to control them through a Bluetooth-connected Wii remote. We also added an external speaker to play sounds and eventually figured out how to power the whole thing safely through a battery pack.
Baby's first roll
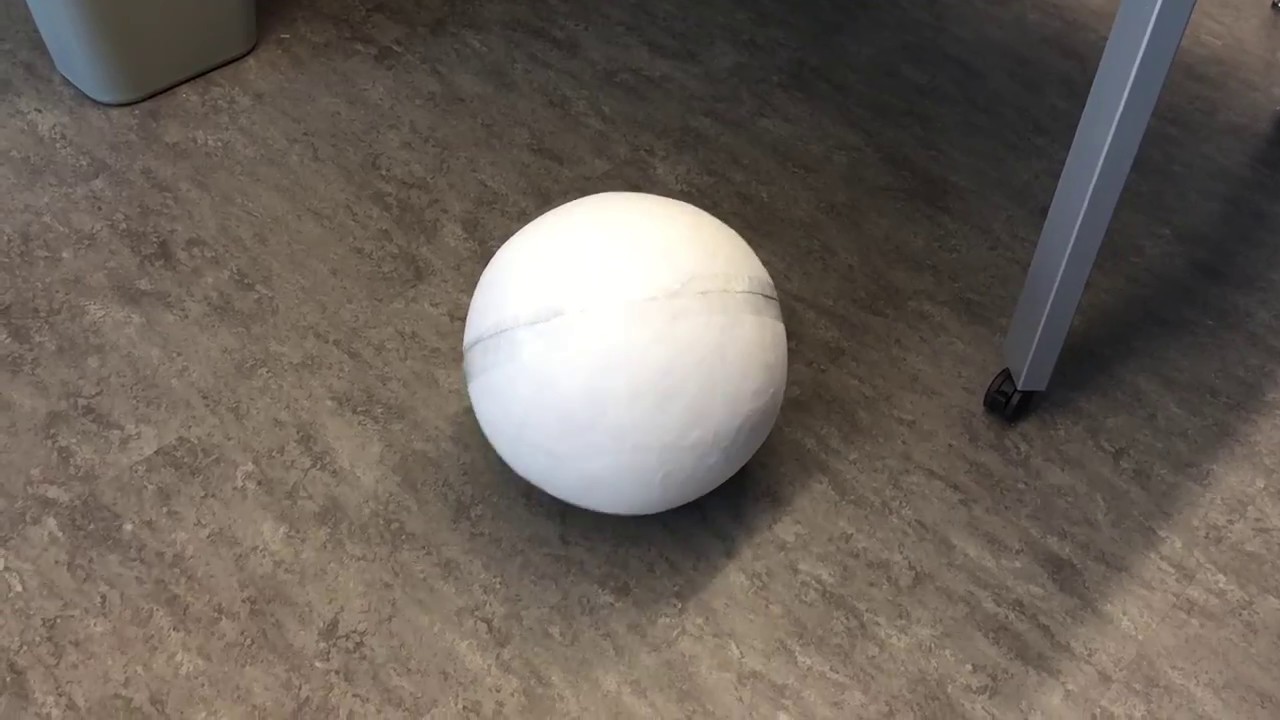
At this point Baby BB-8 looked more like a snowball, but it could roll, make noises, and change directions just like we wanted.
Decorating
We found a nice template image of BB-8's body paint created by Michal Miszta and printed a scaled version on printable vinyl. Although we intended to learn how to cut our vinyl sheets precisely with an electronic vinyl cutter, we ended up cutting the pieces out by hand to save time.
Head problems
Unfortunately but somewhat expectedly, keeping Baby BB-8's head on while rolling became an issue. If the magnetic pull between our platform and the head was too strong the whole thing would seize up and Baby BB-8 would wobble around instead of rolling freely. If it was too weak, the head would slide off and the body would roll away without it.
We spent many hours tweaking the magnetic strength, adjusting the weight of the platform, and oiling up the casters, but we couldn't find the right balance between these variables to make Baby BB-8 roll with its head on like Angelo's prototype could.
The problem seemed to be with our thinner fiberglass shell, which allowed the sphere to flex and contort more than Angelo's paper maché shell did. Without a consistent distance between the head and our inner magnetic platform, keeping the head on was seemingly impossible without adding more layers to our shell or switching to a less flexible material.

Takeaways
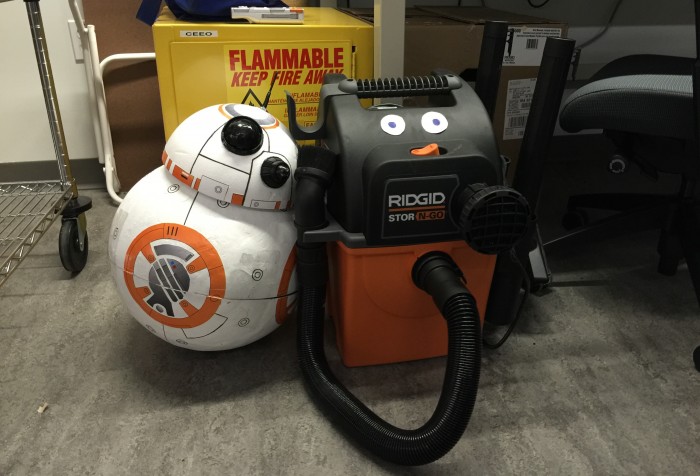
Baby BB-8 with its adoptive father, Mr. Shop-Vac
As imperfect as our Baby BB-8 prototype was, it provided an excellent vehicle for our team of 7 to practice and learn about a wide variety of new skills and technologies, including:
- Fiberglass-making
- 3D modeling, printing, and smoothing
- Laser-cutting
- Metal-cutting
- Soldering
- Vinyl printing
- Raspberry Pi and Python programming
- Electronics power distribution
Just as I did during the Oreo De-Creamer and Tufts Dash projects I made sure to keep each meeting fun, informative, and productive to meet our self-imposed deadlines and provide each student with plenty of opportunities to "learn by making". Thanks in part to the Weekend of Making and Tufts MAKE's growth, this team was also the most multi-disciplinary group in Tufts MAKE's history, providing each student with opportunities to learn from and collaborate with students from entirely different majors and backgrounds.
In 2012 when my co-founders and I started Tufts MAKE we could only dream of having access to the kinds of spaces, tools, and materials that this new team had while building Baby BB-8 four years later. As the "old man" in the group, I sometimes wondered whether the freshmen and sophomore students truly appreciated how much easier it now was to make things at Tufts.
Then, a few days into making BB-8's shell and planning out its electronics, one of the freshmen in the team told me:
"I think I'm starting to get what you mean by 'learning by making'. This is actually pretty cool."
Yes it was, and I'm so glad to have concluded my time as Tufts MAKE's leader with a project that so clearly embodied the kind of interdisciplinary collaboration and hands-on learning that our club was founded on.